Unveiling Alumina Solution: Uses & Benefits You Need To Know
Is alumina solution a revolutionary material, poised to reshape industries and usher in a new era of technological advancement? The multifaceted nature of alumina solutions, encompassing their diverse applications and inherent properties, strongly suggests a resounding "yes." From advanced ceramics to biomedical implants, alumina's versatility is undeniable, making it a cornerstone of innovation across various sectors.
Alumina, chemically known as aluminum oxide (AlO), is a compound renowned for its exceptional physical and chemical properties. Its high melting point, excellent hardness, superior corrosion resistance, and remarkable electrical insulation capabilities contribute to its widespread use. The "solution" aspect in this context, particularly in its use for industrial processes, refers to the dissolving or dispersing of alumina in a liquid medium, allowing for controlled application and manipulation of the material at a microscopic scale. This ability to tailor the material's properties at the molecular level unlocks a broad spectrum of possibilities.
To truly grasp the scope and potential of alumina solutions, one must consider its diverse applications and the inherent challenges in its production and implementation. This necessitates a thorough understanding of its properties, the methods used to create alumina solutions, and its current and prospective applications.
The creation of an alumina solution is, at its core, a process of controlled dispersion or dissolution. While the exact method employed depends on the intended use and desired characteristics of the final product, several key techniques are generally used. These typically involve the use of alumina powder, the selection of a suitable solvent or dispersing agent, and the application of energy to facilitate the process. Various grades of alumina are available, ranging from highly pure, fine powders to coarser, less refined versions. The choice of powder grade is crucial, as it directly affects the final product's properties, such as particle size distribution, surface area, and overall reactivity. It is a delicate balance between the alumina's inherent inertness and the need for it to interact effectively with the chosen liquid medium.
The selection of the dispersing agent or solvent is equally important. The choice is dictated by several factors including the desired application, the compatibility of the alumina with the liquid, and the environmental and safety considerations. Water, organic solvents, and various specialized formulations are frequently used. Surfactants or dispersants are often added to the solution to reduce surface tension and prevent the alumina particles from clumping together, creating a more stable and homogeneous suspension. These additives are critical to ensure consistent performance and prevent defects in the final product.
Once the alumina powder and the dispersing agent have been selected, energy is then typically applied to the system. This may involve techniques such as sonication, ball milling, or high-shear mixing, all designed to break down particle agglomerates, ensuring a fine and uniform dispersion of the alumina. Sonication, using ultrasonic waves, can create intense cavitation, which helps to break up particle clusters. Ball milling involves grinding the alumina powder with ceramic balls in a rotating container, further refining the particle size. High-shear mixing employs powerful impellers to generate strong fluid forces, also promoting dispersion. The choice of energy application method depends on the desired particle size distribution, the volume of the solution, and the desired processing time.
The versatility of alumina solutions is reflected in the range of applications across various industries. In the ceramics industry, it's a vital component in the production of high-performance materials for use in spark plugs, cutting tools, and other wear-resistant applications. These ceramics boast exceptional strength, high-temperature stability, and outstanding resistance to corrosion, making them ideal for harsh environments.
In the field of electronics, alumina solutions are used to produce substrates for integrated circuits and thin-film coatings for a variety of electronic components. The material's excellent electrical insulation properties and thermal conductivity enable it to dissipate heat effectively, making it a crucial material in the operation of modern electronic devices.
The biomedical field also benefits from alumina solutions. They are critical in the production of biocompatible materials, specifically, for implants such as hip and knee replacements, providing superior wear resistance and bio-compatibility. The use of alumina in medical applications leverages its inertness to minimize adverse reactions within the body, and its strength to withstand the mechanical stress associated with movement.
Coatings based on alumina solutions also find widespread application. They offer excellent protection against wear, corrosion, and abrasion, prolonging the lifespan of components in a variety of industries. These coatings are applied using various techniques, including spraying, dipping, and spin coating, allowing for a precise control over the coating thickness and uniformity.
The aerospace industry utilizes alumina solutions to produce high-temperature components. These components can withstand extreme thermal conditions, making them ideal for use in jet engines, rocket nozzles, and other demanding applications, where material performance under stress is paramount.
The research and development community is continuously exploring new applications for alumina solutions. Nanotechnology is a particularly exciting field, as alumina nanoparticles can be incorporated into a variety of materials to enhance their properties. This includes the development of advanced composite materials, coatings with improved functionalities, and drug delivery systems with targeted release capabilities.
The industrial production of alumina solution is a complex process, with several stages involved. The process starts with the procurement of high-purity alumina powder and the selection of suitable solvents or dispersing agents. The powder is then mixed with the liquid medium, usually with additives such as dispersants and stabilizers to ensure a homogeneous suspension.
The mixture then undergoes a dispersion process, which can involve techniques like ball milling, sonication, or high-shear mixing, to break down particle agglomerates and achieve the desired particle size distribution. The particle size is a critical factor, as it influences the final product's properties such as viscosity, stability, and coating performance.
Quality control is a crucial aspect of the industrial process. This involves the measurement of key properties, such as particle size distribution, viscosity, and solid content. The control ensures that the product meets specifications and is suitable for its intended application. Spectroscopic techniques, such as dynamic light scattering (DLS) and X-ray diffraction (XRD) are often employed to characterize the alumina particles and ensure they meet the required specifications.
The scale-up of the production process from the laboratory to industrial scale presents several challenges. This includes maintaining the particle size distribution, achieving consistent product quality, and ensuring safety and environmental compliance. The process requires careful optimization of various parameters, such as mixing speed, temperature, and the addition of additives.
The use of alumina solutions is not without challenges. One of the major hurdles is controlling the particle size distribution. Agglomeration of the alumina particles can lead to defects in the final product, so ensuring uniform dispersion is crucial. This requires optimizing the mixing process and incorporating effective dispersants. The cost of high-purity alumina powder is also a factor, particularly for large-scale applications. Research focuses on developing more cost-effective methods of producing alumina solutions to make them accessible to a wider range of applications. Moreover, there are environmental considerations related to the solvents used in the preparation of alumina solutions, requiring careful selection and responsible disposal.
The future of alumina solutions is very promising. Research and development efforts continue to explore new applications and improve the properties of alumina-based materials. One area of interest is the development of advanced composite materials, where alumina nanoparticles are incorporated into a matrix material to enhance its strength, toughness, and wear resistance. The development of high-performance coatings for a wide range of applications is also a major focus. These coatings are designed to provide protection against corrosion, abrasion, and high temperatures.
Nanotechnology is playing a crucial role in advancing the field of alumina solutions. The ability to manipulate materials at the nanoscale allows for the creation of innovative products with tailored properties. For example, alumina nanoparticles are being explored for use in drug delivery systems, where they can be designed to release drugs in a controlled manner. They are also being used to enhance the performance of solar cells and other renewable energy technologies. Further research into the use of alumina solutions in energy storage systems, such as batteries and fuel cells, is also underway.
The sustainability aspect is becoming increasingly important, and research is focusing on developing greener methods of producing alumina solutions. This includes the use of environmentally friendly solvents and the development of processes that minimize waste. The goal is to create alumina-based materials that are not only high-performing but also have a minimal environmental footprint.
Several companies are actively involved in the production and application of alumina solutions. These companies invest heavily in research and development and are at the forefront of innovation in the field. They offer a wide range of products, including alumina powders, dispersions, and coatings. These companies drive the advancement of alumina solutions, contributing to the development of new applications and the improvement of existing technologies.
The advancement in the use of alumina solutions depends on interdisciplinary collaboration. This includes researchers from materials science, chemistry, engineering, and biomedical sciences working together to develop new applications. The sharing of knowledge and expertise fosters innovation and accelerates the development of new technologies. Governmental agencies and funding organizations also play a critical role, providing financial support for research and development. Their contributions are vital for the advancement of the field.
The outlook for alumina solutions is bright. Continued innovation, a focus on sustainability, and expanding applications in various industries suggest a promising future for this versatile material. As technology continues to evolve, alumina solutions will undoubtedly play a vital role in shaping the future of materials science and various other fields.
Here's a table summarizing the key properties and applications of alumina solutions:
Property | Description | Application Examples |
---|---|---|
High Hardness | Exceptional resistance to scratching and wear. | Cutting tools, abrasive materials, wear-resistant coatings |
High Melting Point | Maintains structural integrity at elevated temperatures. | High-temperature ceramics, furnace linings, aerospace components |
Excellent Corrosion Resistance | Resistant to chemical attack in harsh environments. | Chemical processing equipment, protective coatings |
Good Electrical Insulation | Resists the flow of electricity. | Spark plugs, electronic substrates, insulators |
Biocompatibility | Compatible with living tissues. | Medical implants (hip replacements, knee replacements), dental implants |
High Thermal Conductivity | Efficiently transfers heat. | Heat sinks for electronics, thermal management systems |
Versatile Coating Properties | Can be applied to various surfaces to improve their characteristics. | Wear resistance, corrosion protection, barrier properties |

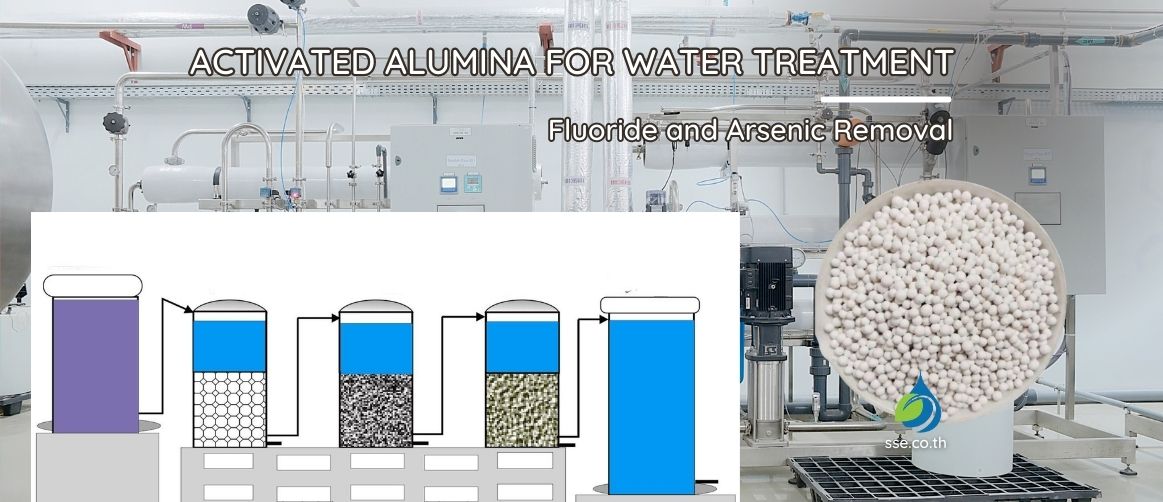
